7. Breathability.
The breathability of a project’s stick-to-skin tape plays a crucial role in how long it will adhere to skin. The moisture vapor transmission rate (MVTR) tells engineers how well tapes allow sweat generated underneath them to escape. MVTR is a function of both the adhesive layer and the tape backing. If sweat isn’t able to get out, it will accelerate the failure of the bond to skin.
The MVTRs typically reported for medical tapes do not apply when the tapes are used beneath most wearables. The devices are typically occlusive (i.e., water and air can’t pass through them) preventing moisture from passing directly through the tape in the z-direction. For this reason, tapes with nonwoven backings, which allow some degree of x-y transmission of moisture vapor beneath the occlusive wearable, may perform better than film-backed tapes that lack this mechanism of moisture transport.
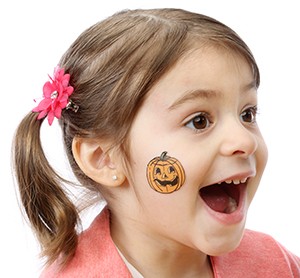
8. Human factors.
When it comes to dealing with babies and toddlers, feedings and changings aren’t the only difficult tasks. Sticking to their skin is also a challenge because it is still very thin and doesn’t yet have the robustness that the skin of older kids or adults has.
Be aware that skin doesn’t stay constant in adulthood either. Similar to babies and toddlers, elderly users have thin skin that is much more fragile than that of a healthy adult in middle age.
For applications requiring wear on fragile skin, silicone adhesives are highly recommended. They’re gentle to the skin, causing minimal pain upon removal, since they pull less at skin or hair when they’re taken off. Silicone adhesives can also be repositioned. For more durable skin, and for devices that require longer wear times, acrylic tapes are the way to go.
9. How the device will be manufactured.
Taking into consideration how you will bond your device to the backing of the stick-to-skin tape from the earliest stages of development can save time and money. We consulted with one manufacturer that had selected a tape with a urethane non-woven backing based on its appearance and feel. The company completed multiple internal wear studies before testing whether the backing was compatible with the thermal-bonding technique their manufacturing group desired to use. Unfortunately, and predictably, the urethane didn’t melt and thus wouldn’t bond. When they came to us for recommendations, we suggested they use a tape with a polyester spunlace backing for heat bonding. Had this been addressed earlier they could have avoided some headaches. Considering early on in the process how a device will be manufactured can help companies avoid redesigns, delays and cost overruns.
10. Sterilization method.
This is another factor that oftentimes is an afterthought until the device is nearly finished. Don’t make that mistake.
There are three main types of sterilization, two of which are radiation-based. They include:
- Ethylene Oxide. This entails putting devices into chambers with the gas, which kills bacteria. It is a time-intensive process, and there’s potential for residual gas.
- E-beam / Gamma Radiation. Radiation is a quick method that can be done in a matter of seconds, and both e-beam and gamma radiation have the effect of killing bacteria. The downside? Radiation exposure alters the performance of most, but not all, adhesives. No silicone adhesives exposed to radiation sterilization will have the same performance. Many acrylic tapes will see a decline in performance as well.
With this is mind, remember to test adhesives that have been exposed to your desired sterilization method early on in development. Testing adhesives without knowing how they will be affected by your sterilization process is, frankly, a waste of time, as you’ll likely get different performance after post-sterilization.
Overcoming Medical Adhesive Obstacles
So, how can a design engineer make sure their next project goes smoothly?
First, talk to adhesives experts early in the process. They are happy to discuss options and suggest a tweak to your construction now that may prevent a redesign later.
Second, consider your stick-to-skin tape holistically. Does the adhesive have the right balance of adhesion and gentleness? Is the backing conformable enough? Does it meet breathability requirements? Having a holistic approach to medical device tapes can help prevent delays and budget overruns. Every time you make a change to address one challenge, review every other aspect of the design for unintended consequences.
Finally, recognize what’s possible. Going into projects with unrealistic expectations of what medical device tapes and adhesives can to do is not helpful. For example, expecting a device that uses a tape capable of 14-day wear to peel off quickly and painlessly after a few days will lead to disappointment, because that’s not possible—yet. Rest assured, development experts are working hard to bring design engineers the next wave of stick-to-skin solutions.
Please direct questions to Kris Godbey, senior applications development engineer in the same 3M division as the author with more than 35 years in product development and stick-to-skin technical support.