Blood glucose test strips are incredibly important for those working to manage diabetes. The strips enable those living or caring for someone with the condition to make life-sustaining decisions while maintaining independent, active lifestyles. In order for the strips to do their job, they must be designed so each layer is able to perform its critical function without interference from other layers or external contamination.
While there are many materials that can be used to design a test strip, the most common are adhesives to bond layers together and hydrophilic materials to promote fluid flow from the chamber entrance to where the assay is measured and evaluated. These two layers play significant roles in the device’s accuracy. Issues can arise during test strip design and manufacturing processes, as well as during the strip’s shelf life. When the individual test layers don’t function well or in combination with the other layers’ materials, strip preference may be impacted.
To help design the most accurate strips possible, you should be aware of five common issues that can arise throughout a test strip’s lifecycle, as well how to manage them.
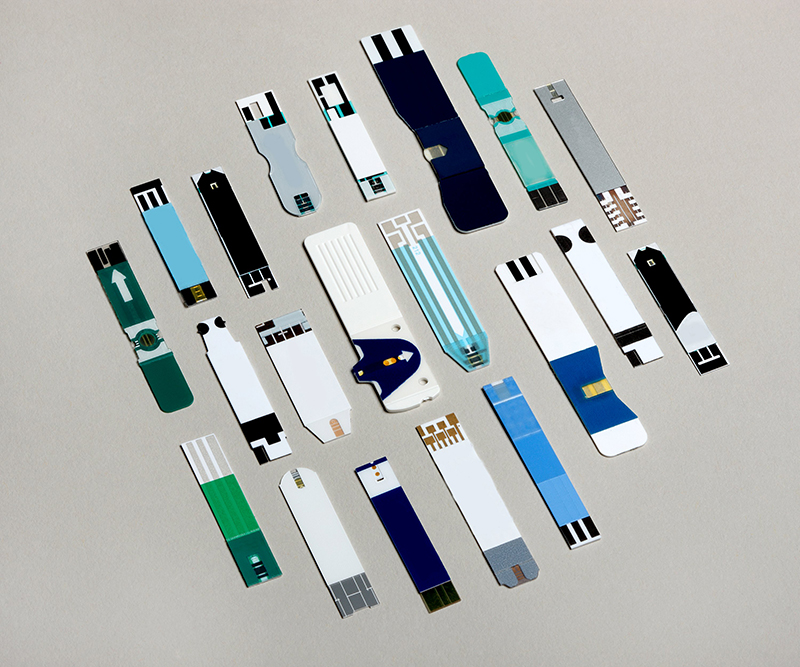
1. Implications of Contaminants or Leeching
Unstable materials or materials that contain contaminants dissolvable by blood could migrate and jeopardize test result accuracy. Contaminants can be introduced in several ways, such as by materials from suppliers, during strip assembly or as a strip degrades from storage conditions.
Tips to mitigate: First and foremost, select materials that are compatible with the assay they will encounter. Additionally, work with your material supplier to measure and certify a material’s purity and composition appropriate for your application. Tier-one suppliers should be expected to properly manage their supply chain and provide evidence that process and design controls are in place to minimize the risk of unintended contaminants.
2. Instability and Aging Effects
Some materials lose performance over time, particularly at elevated temperatures, or may degrade and ultimately influence strip accuracy.
Tips to mitigate: Material stability and aging tests must be completed to know how materials will change over time or under certain conditions. Material suppliers should perform stability studies and demonstrate performance to help guide the material selection process. With stability results, you should choose materials that are stable under the conditions they will experience in their lifetime. Process validation studies, process controls and quality testing are used to ensure materials are consistent from lot to lot. Processing of materials to make the device may also contribute to material stability. It’s important to make sure all equipment is adequately maintained, is in calibration and that proper cleaning procedures are applied before device production.
3. Issues with Adhesives and Spacer Layers
Adhesives and spacer layers are critical to ensuring the right amount of blood makes its way through microfluidic channels. Inconsistent volumes in microfluidic channels can potentially cause measurement errors because reagents may not be present in enough quantities for the device’s design. These layers can also cause measurement errors when there is incomplete coverage, coating voids, adhesive streaks or inconsistent thickness. Many types of coating defects may result in blood leaking from fluidic channels.
Tips to mitigate: Work with an adhesive supplier that can ensure a uniform thickness and uniform coverage to minimize coating defects. Because test strips and other point-of-care diagnostic devices are generally quite small, defects such as streaks and voids are often difficult to measure when material suppliers use industrial-sized production equipment. You can help avoid these challenges by vetting material suppliers up front about their defect detection methods.
4. Adhesive Build-up
Adhesives can build up over time on machine cutting surfaces that are used for slitting and converting operations.
Tips to mitigate: Avoid soft adhesives that are incapable of withstanding the friction and speed of manufacturing processes. Choose an adhesive that is sufficiently stiff to resist deformation and will resist transfer to cutting equipment surfaces while still providing adequate adhesion to the device’s other materials.
5. Damage to substrates and coatings
As with the adhesive and spacer layers, damage to other substrates and coatings during assembly can produce a device that doesn’t function as intended. For instance, if the device relies on optical methods for assay detection, any scratches produced during manufacturing may cause significant surface defects and may produce measurement errors.
Tips to mitigate: To minimize the potential for damage, select processes and machine designs with surface protection in mind. When possible, choose materials that are scratch-resistant or design your process to protect critical material surfaces.
A strip’s overall success in the intended application may come down to the quality and compatibility of materials used in its assembly. Each strip layer should function as expected in combination with other layers to produce a more accurate test result. One of the best ways to avoid issues throughout a strip’s lifecycle involves choosing the right materials for your device design. Consult with your materials supplier and learn the best practices for designing an accurate test strip before embarking on your next test strip design.