Additive manufacturing is experiencing an unprecedented period of growth in the medical device industry. No longer limited to prototyping, additive manufacturing is being used to create everything from patient-specific surgical guides to custom-fit prostheses to implants and 3D-printed tissue.
In 2012, 16.4% of revenue in the additive manufacturing industry came from medical applications. By 2019, the global market for 3D-printed medical devices is expected to exceed $965 million.1,2 This huge opportunity for breaking barriers also comes with considerable risks, as industry pioneers experiment with unusual materials and unique methods.
Unmitigated creativity is pushing the boundaries of possibility, while regulatory science establishes clear methods for assessing the consistent performance of additive manufacturing processes and substances when used in demanding medical environments.
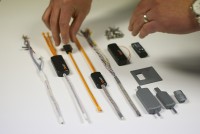
In the meantime, the stringent requirements posed by medical device developers remains a challenge. Customization and novel uses have made meeting current FDA regulations surprisingly uncomplicated for additive manufacturers thus far, but medical device developers are still accountable for final product performance—and additive manufacturing vendors that specialize in medical materials are few and far between.
Despite these challenges, modern and versatile additive manufacturers can expedite, and improve the R&D. Additionally, advances that sound like they’ve jumped right out of the pages of a science fiction novel are manipulating materials and methods in ways that could transform even more conservative applications.
Consider these factors—creativity, advances in materials, science and research in medicine; they make clear that now is the perfect time to explore how additive manufacturing can benefit the medical device industry.
1. Create A Product Real Customers Want To Buy
The need to please a diverse customer base, coupled with the highly regulated and specialized nature of device development, has driven industry leaders to ditch the traditional approach to getting a product to market. Instead, they’re not only saving time and money, but also are presenting products that are more appropriate to meeting the demands of a complicated group of clients and users: By replacing the linear path from design to manufacturing to marketing with an iterative or evolutionary design process.
Vendors that marry traditional manufacturing knowledge with rapid prototyping via additive manufacturing offer a nimble approach to device design. This experience allows developers to provide multiple mechanical solutions to a single problem or to pivot development to suit the most appropriate manufacturing methods and demands of the market.
Devices created entirely by additive manufacturing can also evolve based on real-time feedback from customers. Short production runs of specialized products are both affordable and attainable with additive manufacturing, giving medical device developers the freedom to release a beta version into the market and move it back into the design cycle before committing to a larger production run.
2. More Accuracy in Biomimicry
When simulated use of a medical device is required for complicated or dynamic internal functionality, anatomical models are an ideal way to challenge a design. No two individuals are the same, nor are their organs.
Precise replicas of human anatomies that capture unique internal and external features can be created with 3D-printing techniques. Multiple simulated anatomical models that represent a range of “normal” environments can be created quickly and affordably for medical device design evaluation as well as for form, fit and functional testing.
The geometric freedom and multi-material printing abilities of additive manufacturing puts far fewer design constraints on device manufacturers. For external prosthesis, the manufacturing technique creates exceptionally precise and refined replication of unique shapes to deliver parts and pieces that more accurately fit the first time around, which can eliminate time-consuming validation and modification processes.
3. Deliver Exceptional Comfort
With additive manufacturing techniques, medical device designers and engineers can create extremely lightweight, small or low-profile designs to maximize comfort and freedom of movement for patients or physicians.
Intricate yet durable honeycomb patterns and parts with open, rather than dense interiors are achievable and enable the reduction of weight without sacrificing strength or shape. Complex geometries with tight tolerances or exceptionally small builds can also be fashioned, keeping surgical tools streamlined or devices that are worn as sleek and unobtrusive as possible.
4. Break Through Barriers With New Materials, New Methods
The number of materials currently certified for use in and around the human body is limited. In addition, the cost for certified materials specific to additive manufacturing use is significantly higher compared to traditional manufacturing processes. However, because materials are seen as a major constraint for additive manufacturing, they have become the focus of research and development efforts across the industry.
How materials and binding agents react to clinical demands and affect biological processes are continual concerns and a particular target of innovative advances. For example, 3-D printed parts are notoriously directionally dependent when it comes to strength and resilience. New resins that express strength in all directions can offset challenges related to the layered nature of additive manufactured parts, and new methods are producing better homogenization and enhanced durability in final products.3
Bioprinting (creating organs or tissue using 3D printing machines) seems to get the bulk of the media attention as it related to new medical materials developed by the additive manufacturing industry, but it is far from being curtain ready.4 In the meantime, materials that express biomimicry are currently being used by research hospitals for procedures such as cranial implants to decrease operation time and reduce complications, for example.5
The most common materials for end-use medical devices today are stereolithography (SLA) resins that are USP Class 6 certified; a number of metals, including stainless steel, titanium; and some super alloys used in direct metal laser sintering (DMSL). Medical SLA resins are certified for contact applications such as custom-designed surgical tools or device components but not for embedded applications.
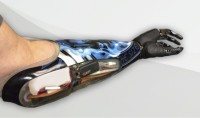
For medical devices that have zero contact with internals or fluids—such as robots that deliver medication or cases that house electronics for functional prosthetics—certified medical-grade materials aren’t necessarily required. However, finding more materials that are not just medical grade, but biocompatible and sterilization-stable is a key priority for advancing the usability of additive manufacturing in medical device development.6
The Future of Additive Manufacturing
Advances are highly dependent on a close relationship between additive manufacturing firms and medical device design and manufacturing teams. Communicating design intent, detailing strength requirements, and including extensive information about what will happen to the final product in the clinical setting are essential to ensure that the right combinations of technologies are used, and that the final product meets the rigorous requirements of the medical device industry and the customers in which it serves.
References
- Snyder, G.H., Cotteleer, M.J., and Kotek, B. (April 28, 2014). 3D Opportunities in Medical Technology, Deloitte University Press. Accessed August 12, 2015. Retrieved from http://dupress.com/articles/additive-manufacturing-3d-opportunity-in-medtech/
- Did You Know, Additive Manufacturing for Medical, Bioprinting and Drug Discovery. Accessed August 12, 2015. Retrieved from http://www.additivemanufacturingmedical.com/
- “Toward Isotropically Tough 3D Printed Biomedical Devices,” Design of Medical Devices Conference presentation abstract. Accessed August 12, 2015. Retrieved from http://www.dmd.umn.edu/2015/additivemfg.html
- “Medical Applications for 3D Printing: Current and Projected Uses,” PMC US National Library of Medicine. Accessed August 12, 2015. Retrieved from http://www.ncbi.nlm.nih.gov/pmc/articles/PMC4189697/
- Wiltz, C. (August 21, 2014). The First FDA-Cleared, 3-D Printed Facial Implant. MD+DI. Accessed August 12, 2015. Retrieved from http://www.mddionline.com/article/first-fda-approved-3-d-printed-facial-implant-140821
- Pink, J. (March 6, 2015). Risks of Additive Manufacturing: A Product Safety Perspective. EMDT. Accessed August 12, 2015. Retrieved from http://www.emdt.co.uk/daily-buzz/risks-additive-manufacturing-product-safety-perspective